ISO 10370:2014 pdf download.Petroleum products — Determination of carbon residue — Micro method
This International Standard specifies a method for the determination of the amount of carbon residue, in the range 0,10 % (m/m) to 30,0 % (m/m), left after evaporation and pyrolysis of petroleum products under specified conditions. NOTE 1 The carbon residue value serves as an approximation of the tendency of petroleum products to form carbonaceous deposits under similar degradation conditions, and may be useful in the assessment of relative carbon-forming tendencies of products within the same class. In this case, care should be taken in the interpretation of results. For products which yield a residue in excess of 0,10 % (m/m), the test results are equivalent to those obtained by the Conradson carbon residue test (see ISO 6615 [1] ) in the range of 0,10 (m/m) to 25,0 (m/m) (for details see Annex A).
This International Standard is also applicable to petroleum products which consist essentially of distillate material, and which may yield a carbon residue below 0,10 % (m/m). On such materials, a 10 % (V/V) distillation residue is prepared by the procedure described in 7.3.1 and 7.3.2 before analysis. Both ash-forming constituents, as defined by ISO 6245 [2] and non-volatile additives present in the sample add to the carbon residue value and are included in the total value reported.
NOTE 2 The presence of organic nitrates incorporated in certain distillate fuels will yield abnormally high values for the carbon residue. The presence of alkyl nitrate in the fuel may be detected by ISO 13759. [3]
2 Normative references
The following documents, in whole or in part, are normatively referenced in this document and are indispensable for its application. For dated references, only the edition cited applies. For undated references, the latest edition of the referenced document (including any amendments) applies. ISO 3405, Petroleum products
— Determination of distillation characteristics
3 Terms and definitions
For the purposes of this document, the following term and definition apply 3.1 carbon residue the whole residue produced of a sample from the specific conditions of evaporation and pyrolysis described in this International Standard
4 Principle
A weighed aliquot of the oil sample is placed in a glass vial and heated to 500 °C under an inert (nitrogen) gas stream in a controlled manner for a specific time. Volatiles formed during the reactions are swept away by the inert gas. The carbonaceous residue remaining is weighed.
5 Reagents and materials
5.1 Nitrogen, low oxygen content, i.e. 99,998 % (V/V) or better, with appropriate regulation to providea delivery pressure of 0 kPa to 200 kPa.
NOTE The practical minimum delivery pressure is 140 kPa.
6 Apparatus
6.1 Glass sample vials, of 2 ml capacity, 12 mm outside diameter, approximately 35 mm high.
A vial of 4 ml capacity, 12 mm outside diameter, approximately 72 mm high may be used with samples ofvery low carbon residue content, i.e. below approximately 0,20 % (m/m), but no precision data has been obtained for them.
NOTE 1 An interlaboratory study [4] has been carried out by the Energy Institute on the 10 % volume distillation residue procedure for middle distillates using 4 ml vials and automatic distillation units and the precision is given in Clause 12.
NOTE 2 A glass sample vial of approximately 20 ml capacity (20,5 mm to 21 mm outside diameter by (70±1) mm high) for samples that are expected to yield residues < 0,10 % (m/m) may also be used, so that a more appreciable mass difference may be determined. In this case, a 5 g sample size is suggested. No precision has been determined for this technique, but it may be found suitable for very low 10 % residue samples.
6.2 Eyedropper or small rod, suitable for sample transfer.
6.3 Coking oven, comprising a circular heating chamber approximately 85 mm diameter by 100 mm deep for top-loading, capable of heating to 500 °C at a rate of between 10 °C and 40 °C per min, with exhaust port of 13 mm inside diameter for nitrogen purge of oven chamber (inlet near top, exhaust at bottom centre), with thermocouple sensor located in oven chamber next to but not touching sample vials, and with lid capable of sealing out air.
The condensate outlet leads into a short vertical section where most of the vapour condenses and falls into a removable trap located directly below the oven. A schematic diagram is given in Figure 1.
6.4 Sample vial holder, comprising a cylindrical aluminium block approximately 76 mm diameter by 17 mm thick with 12 evenly spaced holes (for vials) each 13 mm diameter by 13 mm deep.
The holes shall be arranged in a circular pattern approximately 3 mm from the perimeter. The holder shall have legs 6 mm long with guides to centre in the oven chamber, and an index mark on the side to use as position reference. A typical holder is shown in Figure 2.
6.5 Thermocouple, iron-constantan, with exterior read-out and a range including 450 °C to 550 °C.
6.6 Analytical balance, of 0,1 mg sensitivity.
6.7 Cooling vessel, desiccator or similar tightly closed vessel, without desiccant.ISO 10370 pdf download.ISO 10370-2014 pdf download
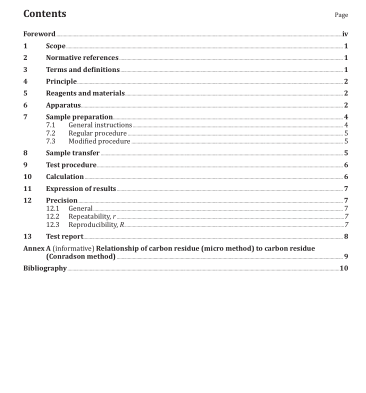