ISO 23472-4:2022 pdf download.Foundry machinery — Vocabulary — Part 4: Abrasive blasting machines and other equipment related to cleaning and finishing for casting
This document defines a set of terms and definitions of abrasive blasting machines and other equipment related to cleaning and finishing for casting in foundry machinery.
It applies to standard development in the foundry machinery field, technical documentation, related scientific and technical publications, etc.
2 Normative reference
There are no normative references in this document.
3 Terms and definitions
For the purposes of this document, the following terms and definitions apply.
ISO and IEC maintain terminology databases for use in standardization at the following addresses:
— ISO Online browsing platform: available at https:// www .iso .org/ obp
— IEC Electropedia: available at https:// www .electropedia .org/
3.1 abrasive blasting
shot blasting
process in which workpiece to be cleaned or surface to be treated is subjected to continuous attack by abrasive media (3.4) to achieve a desired result
[SOURCE: ISO 23472-1:2020, 3.1]
3.2 abrasive blasting machine
shot blasting machine
machine used for abrasive blasting (3.1) by either centrifugal force or compressed air to accelerate abrasive media (3.4)
Note 1 to entry: Terms “abrasive blasting machinery”, “shot blasting machinery” are used to address the same assembly of machines.
3.3 abrasive cut-off machine
grinding cutter
device for cutting gate and riser of castings or other metal materials with a high-speed rotating grinding wheel (3.84)
3.4 abrasive media
shot blasting media
granular metallic or non-metallic material to be forcibly applied to a surface to achieve a desired result
Note 1 to entry: Classification of metallic abrasives is provided in ISO 11124-1, and of non-metallic abrasives in ISO 11126-1.
[SOURCE: ISO 23472-1:2020, 3.3]
3.5 abrasive media recirculating system
system in abrasive blasting machine (3.2) that collects the mixture of abrasive media (3.4) and abrased material, separates the abrasive media (3.4) from this mixture, and supplies it to the blasting process Note 1 to entry: This system usually consists of bucket elevator (3.25), screw conveyor, abrasive media separator (3.6), vibrating screen, storage hopper, switch valve (3.72), pipe, etc.
3.6 abrasive media separator
device that removes impurities from used abrasive media (3.4) and separates reusable abrasive media (3.4) by means of gravity, air stream, mesh screen and/or magnetic force
3.7 abrasive media throughput rate
abrasive media flow rate
amount of abrasive media (3.4) blasted by the wheel blaster (3.86) or air blaster (3.8) in unit time during abrasive blasting (3.1)
Note 1 to entry: Usually in minutes as unit time.
3.8 air blaster
assembly consisting of blast nozzle(s) (3.16), blast pot(s) (3.17) and connected hose(s) or tube(s), which accelerates abrasive media (3.14) by pressurized air
3.9 air blasting machine
abrasive blasting machine (3.2) that uses air blaster (3.8)
3.10 air chipper
hand-held pneumatic tool for removing flashes, burrs and raised defects of castings
3.11 automatic cleaning cell
system that automatically completes the cleaning process of castings by robots, manipulators, machine tools, etc.
Note 1 to entry: It is equipped with a tool library, and the robot can automatically replace cleaning tools according to the requirements of the program.
3.12 band cutting machine
band saw
device for cutting gate and riser of castings with ring endless band
Note 1 to entry: It is usually used to cut gate and riser of castings made of light weight metal.
3.13 blade
vane
component of wheel blaster (3.86) that receives and blasts abrasive media (3.4)
3.14 blast gun
rod-shaped component connected to the outlet end of blast hose (3.15) of air blaster (3.8) for holding or clamping, holding the blast nozzle (3.16) at the outlet
3.15 blast hose
blast tube
hose or tube connecting a nozzle to the blast pot (3.17)
3.16 blast nozzle
component connected at the outlet of the blast gun (3.14) with the desired shape, size and abrasive resistance which determines the abrasive media (3.4) flow and angle
3.17 blast pot
blast hopper
container of air blaster (3.8) for storing abrasive media (3.4)
3.18 blasting angle
angle between the centre line of the abrasive beam ejected from the nozzle and the surface of the workpiece being blasted during abrasive blasting (3.1)
3.19 blasting chamber
chamber of abrasive blasting machine (3.2) which contains the workpiece and also prevents the abrasive media (3.4) from escaping to the environment after impacting on the workpiece
3.20 blasting density
amount of abrasive media (3.4) blasted per unit area within the surface that has been impacted by the abrasive media (3.4)
3.21 blasting distance
distance between the nozzle and the surface of workpiece to be blasted during abrasive blasting (3.1)
3.22 blasting pattern
effective area of workpiece surface covered by abrasive beam blasted by wheel blaster (3.86)
3.23 blasting pressure
working pressure of compressed air fed into nozzle or in blast pot (3.17) during compressed-air abrasive blasting (3.29)
3.24 bogie decoring machine
decoring machine (3.36) that uses bogie to transport workpieces
3.25 bucket elevator
continuous conveyor that uses a series of bucket shaped hoppers uniformly fixed on the endless circular traction component to vertically lift abrasive media (3.4), foundry sand and impurities.ISO 23472-4 pdf download.ISO 23472-4 pdf download
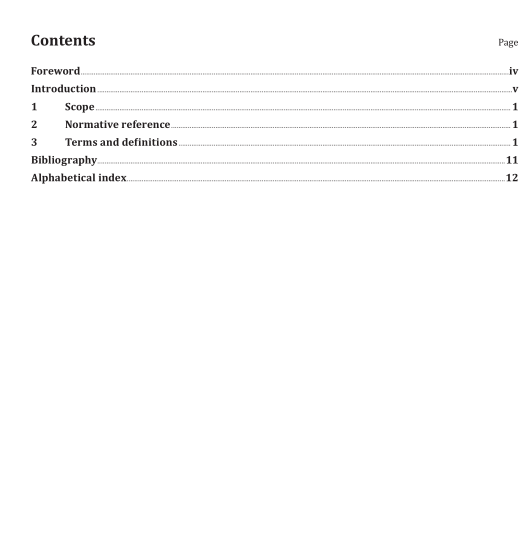