ISO 17463:2022 pdf download.Paints and varnishes — Guidelines for the determination of anticorrosive properties of organic coatings by accelerated cyclic electrochemical technique.
5 Apparatus
Use the electrochemical equipment specified in ISO 16773-2. 6 Specimens 6.1 Samples preparation Proper preparation and preconditioning of coated specimens is critical for successful and reliable experimental data.
6.2 Environmental control
The coating should be applied and cured in accordance with the manufacturer’s recommendation unless otherwise agreed upon between the parties involved. The film thickness should be as uniform as possible. T
he exact film thickness should be measured and reported (e.g. in accordance with ISO 2808). Temperature and humidity control during the application, curing, conditioning and measurement of organic coatings is crucial for a proper determination of the coating resistance. For reliable measurements, temperature control should be equal to or better than ±1 °C. For conditioning prior to measurement, an accuracy of ±2 °C is sufficient for most cases. Each specimen should be kept under controlled conditions in order to prevent post-curing, degradation or any unintended irreversible modification of the coating.
The temperature of the specimens during measurements should be maintained constant to within ±2 °C, preferably within ±1 °C, at 23 °C, if not otherwise specified. Relative values for comparison between specimens outside these guidelines are acceptable if all the specimens are run under the same conditions. When the coating capacitance is the main parameter of interest, control of relative humidity during specimen conditioning is very important. To ensure accurate conditioning, the humidity should be (50 ± 5) % in accordance with ISO 3270, if not otherwise agreed.
6.3 Number of specimens and repeatability of results
Coatings are materials with certain inherent properties: holidays, inhomogeneous film thickness, and non-uniform distribution of pigments, fillers and other constituents.
It is therefore necessary to test more than one panel. In most cases, a minimum of three replicate specimens is necessary for reliable results. It should be checked whether the uniformity between the different specimen plates is sufficient.
It is quite common to find repeatability better than 10 % between the capacitance of replicate specimens, but it depends on the type of coating and the conditions of measurement. More replicates might be necessary to overcome uniformity problems. Such checks should be the responsibility of the operator and should also be agreed between the parties involved. Specimens undergoing a rapid change, caused by weathering or other effects producing degradation, can show a larger fluctuation and therefore a lower repeatability.
7 Procedure
7.1 EIS measurement Perform the EIS measurement as specified in ISO 16773-2.
7.2 Cathodic polarization Set a more negative d.c. potential (see Figure 1) that allows the hydrolysis of the water at the pH of the electrolyte e.g. approximately −1 V (SCE [saturated calomel electrode]) at pH 7. Additionally, this potential should be fixed depending on the impedance of the coating; the larger it is the larger should be the magnitude of the applied cathodic potential. In general, potentials are applied in the range of −2 V to −4 V. The cathodic polarization time varies depending on the quality of the coating. For high quality coatings with long term anticorrosive properties polarization time is typically between 20 min and 60 min.
7.3 Relaxation process
Disconnect the potentiostat and measure the relaxation potential over the time. The time is typically between 160 min and 180 min. If the time of relaxation is too short, the equilibrium will not be reached and EIS measurement is therefore not valid. If this time is too long, the system will evolve due to the migration of ions and the electrochemical reactions at the metallic substrate. The study of the potential relaxation over time can provide useful information about the quality of the coating system, e.g. whether the cathodic reaction producing hydrogen (H 2 ) has taken place during the polarization. Hydrogen production can indicate a poor coating quality. For interpretation of the plots, see References [3] and [6].
7.4 Number of cycles
The cycle involving cathodic polarization/relaxation/EIS can be repeated either up to the degradation of the coating or it is possible to apply a given number of cycles. The number of cycles commonly used is 6. If no differences can be detected with 6 cycles, their number should be increased.ISO 17463 pdf download.ISO 17463 pdf download
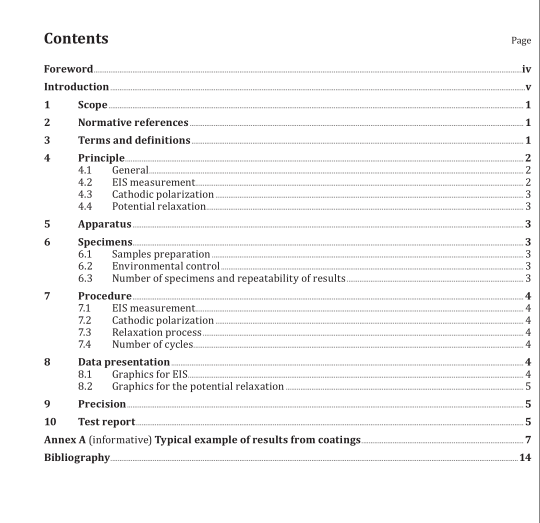