EN ISO 9053-2:2020 pdf download.Acoustics ‑ Determination of airflow resistance ‑ Part 2: Alternating airflow method (ISO 9053‑2:2020)
The sound measuring device shall have a small bandwidth around the piston frequency for reducing background noise and harmonic distortions. For all related measurements at a particular piston frequency including measurement of background noise, the bandwidth of the sound measuring device shall not be changed.
The sound measuring device may be a sound level meter, including microphones and cables, conforming to the requirements of IEC 61672‑1 class 1 or class 2, and with fractional‑octave band filters meeting the requirements of IEC 61260‑1 class 1 or class 2.
It is important that the sound measuring device only measure the sound with frequencies close to the frequency of the piston in order to reduce the effect of harmonic distortions and background noise. The band limiting function can be obtained by the use of a fractional‑octave band filter or FFT‑analyser/technique.
NOTE The sound measuring device is mainly used to determine the difference in sound pressure levels for sound with a constant frequency. Level linearity performance at this frequency is therefore the most important property.
6.4 Vessel and measurement cell
The vessel and the measurement cell shall be in the shape of a circular cylinder or a rectangular parallelepiped (preferably with a square cross‑section in the latter case). The vessel shall include appropriate seals to enable a leak‑free mounting of the airtight termination and the measurement cell.
The vessel and the airtight termination shall be sufficiently stiff to avoid volume changes under alternating pressure conditions.
The volume, V , of the air cavity inside the closed vessel with the airtight termination mounted shall include all connecting pipes, such as to the microphone and to the piston. The piston shall be in centre position when the volume is measured.
The diameter or smallest edge of the measurement cell shall be chosen depending on the specimens to test. In any case, the minimum diameter or smallest edge of the measurement cell shall be 29 mm. Furthermore, the air cavity shall have a cross section that is at least the same as the cross section of the measurement cell. Various measurement cells can be used as long as they fulfil all the requirements of this document. The vessel and the measurement cell should be made so that the airflow is along the flow direction to be measured. This is normally perpendicular to the surface of the specimen to be measured. The measurement cell may include two grills or perforated plates for keeping the test specimen in position. It is important that the test specimen do not move due to the alternating air flow. The supports shall have an open area of minimum 50 %, evenly distributed.
The holes in the support shall have a diameter of not less than 3 mm. The airflow resistance of the support should be less than 1 % of the airflow resistance to be measured. See Annex D for additional information.
6.5 Device for measuring the static pressure
The device for measuring the static pressure shall be capable of performing measurements with a low uncertainty. The uncertainty in the static pressure shall be considered in the uncertainty budget.
6.6 Device for measuring the frequency of the piston
The frequency of the piston shall be determined with low uncertainty. The uncertainty in the frequency shall be considered in the uncertainty budget. The frequency may be measured from the microphone signal by the use of a frequency counter or by frequency analysis.
7 Test specimens
7.1 Homogeneity of test specimen
The test specimen can have different airflow resistivities for different orientations of the specimen relative to the applied direction of airflow. If the specimen is not homogeneous, one or more appropriate orientations shall be selected and described in the test report.EN ISO 9053-2 pdf download.EN ISO 9053-2 pdf download
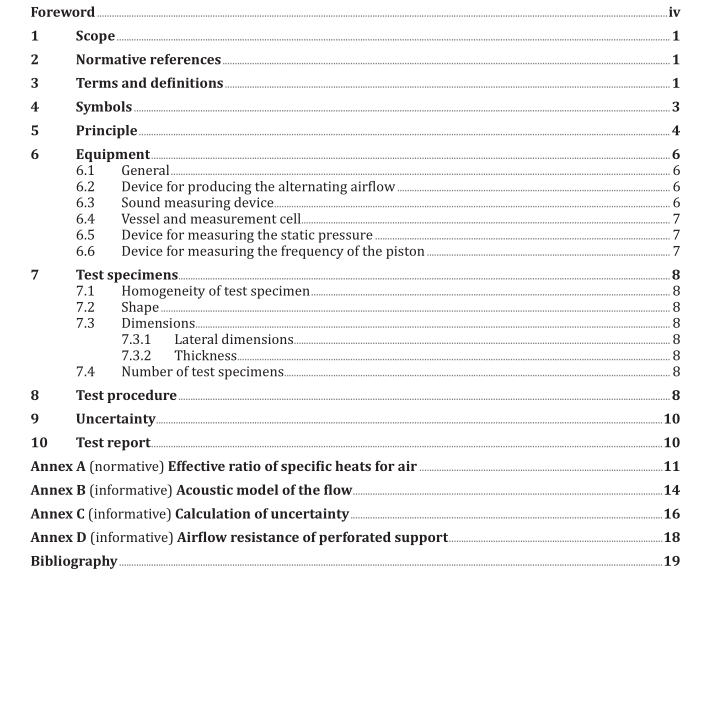